Professional Recommendations on What is Porosity in Welding and Exactly How to Address It
Porosity in Welding: Identifying Common Issues and Implementing Finest Practices for Prevention
Porosity in welding is a pervasive issue that often goes undetected until it causes significant problems with the integrity of welds. This common problem can compromise the toughness and toughness of welded frameworks, posturing security dangers and bring about pricey rework. By recognizing the origin causes of porosity and executing efficient prevention approaches, welders can significantly improve the high quality and dependability of their welds. In this discussion, we will explore the vital variables adding to porosity formation, analyze its harmful results on weld performance, and talk about the most effective techniques that can be taken on to reduce porosity occurrence in welding procedures.
Typical Reasons For Porosity

Using dirty or wet filler products can introduce contaminations right into the weld, adding to porosity problems. To minimize these typical causes of porosity, extensive cleansing of base metals, appropriate securing gas selection, and adherence to optimal welding parameters are important practices in achieving premium, porosity-free welds.
Influence of Porosity on Weld High Quality

The presence of porosity in welding can dramatically jeopardize the structural honesty and mechanical residential properties of welded joints. Porosity produces spaces within the weld metal, damaging its general toughness and load-bearing ability.
Welds with high porosity levels have a tendency to show reduced impact toughness and decreased capacity to warp plastically prior to fracturing. Porosity can restrain the weld's capacity to efficiently transmit forces, leading to premature weld failure and prospective safety dangers in critical frameworks.
Ideal Practices for Porosity Prevention
To improve the structural stability and top quality of welded joints, what specific actions can be executed to reduce the incident of porosity throughout the welding procedure? Making use of the correct welding technique for the certain material being bonded, such as adjusting the welding angle and weapon position, can further avoid porosity. Normal examination of welds and immediate remediation of any problems recognized during the welding process are important practices to prevent porosity and generate high-grade welds.
Value of Correct Welding Strategies
Applying correct welding strategies is extremely important in guaranteeing the structural integrity and top quality of welded joints, building on the structure of effective porosity avoidance steps. Welding strategies directly affect the total strength and sturdiness of the welded structure. One essential aspect of correct welding strategies is preserving the right heat input. Extreme warm can cause raised porosity as a result of the entrapment of gases in the weld pool. Conversely, inadequate warm might lead to insufficient fusion, creating possible weak points in the joint. In addition, using the appropriate welding criteria, such as voltage, present, and travel rate, is critical for achieving sound welds with very little porosity.
Additionally, the option of welding procedure, whether it be MIG, TIG, or stick welding, should align with the particular demands of the task link to guarantee optimum results. Correct cleaning and preparation of the base steel, as well as choosing the appropriate filler material, are likewise crucial components of proficient welding techniques. By adhering to these ideal methods, welders can decrease the risk of porosity formation and create high-grade, structurally sound welds.
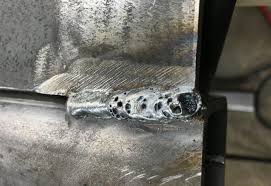
Examining and Quality Assurance Steps
Quality assurance actions play an essential function in validating the honesty and dependability of welded joints. Evaluating treatments are necessary to discover and stop porosity in welding, guaranteeing the stamina and toughness of the end product. Non-destructive screening approaches such as ultrasonic screening, radiographic screening, and aesthetic inspection are typically utilized to determine prospective flaws like porosity. These strategies permit the analysis of weld high quality without compromising the stability of the joint. What is Porosity.
Post-weld evaluations, Going Here on the other hand, analyze the final weld for any defects, consisting of porosity, and verify that it meets defined requirements. Implementing a thorough high quality control strategy that includes thorough screening procedures and examinations is vital to decreasing porosity concerns and making sure the overall high quality of welded joints.
Final Thought
Finally, porosity in welding my latest blog post can be a typical issue that influences the quality of welds. By identifying the usual reasons of porosity and applying ideal techniques for avoidance, such as proper welding methods and screening measures, welders can make certain high quality and reliable welds. It is essential to focus on avoidance techniques to reduce the event of porosity and maintain the honesty of bonded frameworks.